I decided to take screenshots of a new build and a do a little walk thru with Y'all on it....
The problem needing a fix is a dangling inline speed control on my air scrubber. Adhesives simply wont work due to a rough and painted surface. Tried double sided tape and velcro, both failed. Could go buy little screw on cord clips but having a 3D printer, I can do better than that!
So I'm going to design and print a cradle that will keep the speed controller attached to the wall and help keep it more organized.
To start I go to Tinkercad, click on my profile, click new design, and it opens up a new work plane.
On this page you can see the name of the project in the upper left corner, a menu of starter shapes on the right side of the plane, and various buttons across the upper tool bar.
First thing to do is change the name to something recognizable in the upper left corner.
Everything is mouse controlled so it's all click and drag or click and type
After changing the name, to start I click and drag the cube from the shapes menu onto the work plane. You see some basic shapes in the menu but that's just a small sample. There are hundreds of starter shapes to choose from but since this is a basic design, the cube and cylinder are all that's needed.
Looking at the cube there's 5 little white boxes which designate Height x Width x Depth. Above the cube is a little black cone. Clicking on that will raise or lower the project from the work plane. And the little curved arrows around the cube are to turn and flip it.
I click on the little white boxes and change the dimensions of the cube. I believe this one was 105mm x 35mm x 5mm
So that gives me the back. Now I'm going to do the same thing. Click and drag another cube onto the work plane and change it's dimensions.
Now I'm going to move the base and join it up to the back wall
Next, the side walls. Same routine, however when needing two identical parts I only have to make one. After making it you can see in the upper left corner some buttons. The button that looks like stacked pages next to the trash bin is the duplicator button. Clicking that button will produce a mirror image of a part so I do not have to reshape two parts, just the one and then duplicate it.
Now is where some magic happens. These next shapes I work with represent holes and is the way to cut holes or shapes into the project
I have a cylinder hole and cube hole so for the cylinder which will be the hole where a screw will go thru to mount the cradle to the wall I reshape the cylinder, turn it on it's side, and elevate it up off the work plane
Next I do similar steps with the cube and move it into position but again since I need two, I only do one then click the duplicator button.
Looks crazy right? Well we're almost done! The model is complete and ready to export so I click on the export button in the upper right corner and it brings up a menu of what format I want the download. For this it's .STL
Next, on my computer tool bar I click on downloads and it will show me the new file. I click on the file to open and it will open the file with the Creality Slicer program installed in my pc.
And once open in the slicer here's how it looks
Now that it's in the slicer it becomes one object rather than a bunch of parts tied together. Within the slicer I can do a lot more...I can change it's size and multiply it. I can also click a drop down menu and change it's density, printing temp, how it adheres to the printer, and much more. But since this is a basic one off print with no further adjustments needed outside basic default settings it's ready to go.
So I click slice which turns the print into a G-code the printer can read which is kinda like a GPS road map for the printer to follow. After clicking slice then it's time to save the G-Code onto a micro SD card
From there the SD card goes from the pc and into the printer. Hit print and it will show menu options from the card then I just find the project and click print again.
After 4 hours on the printer, I have my new cradle
Then after installation, the issue of a dangling speed controller is remedied!
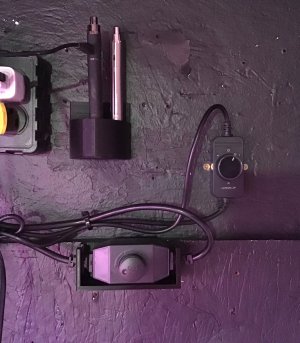